When we set out to design or upgrade motor-driven systems, there's a multitude of decisions to make. One of the most pivotal is the choice of a motor starting method. Today, the Variable Frequency Drive (VFD) has made its presence known in the motor control industry. But what makes it so popular?
Variable Frequency Drives offer a seamless and efficient way to control motor speed and torque during start-ups. It provides adjustable frequency and voltage to the motor, ensuring soft starts, controlled acceleration, energy savings, and longer equipment lifespan.
With a myriad of options out there, why are companies like ours—SAKO—giving VFDs a nod? Let’s dive in.
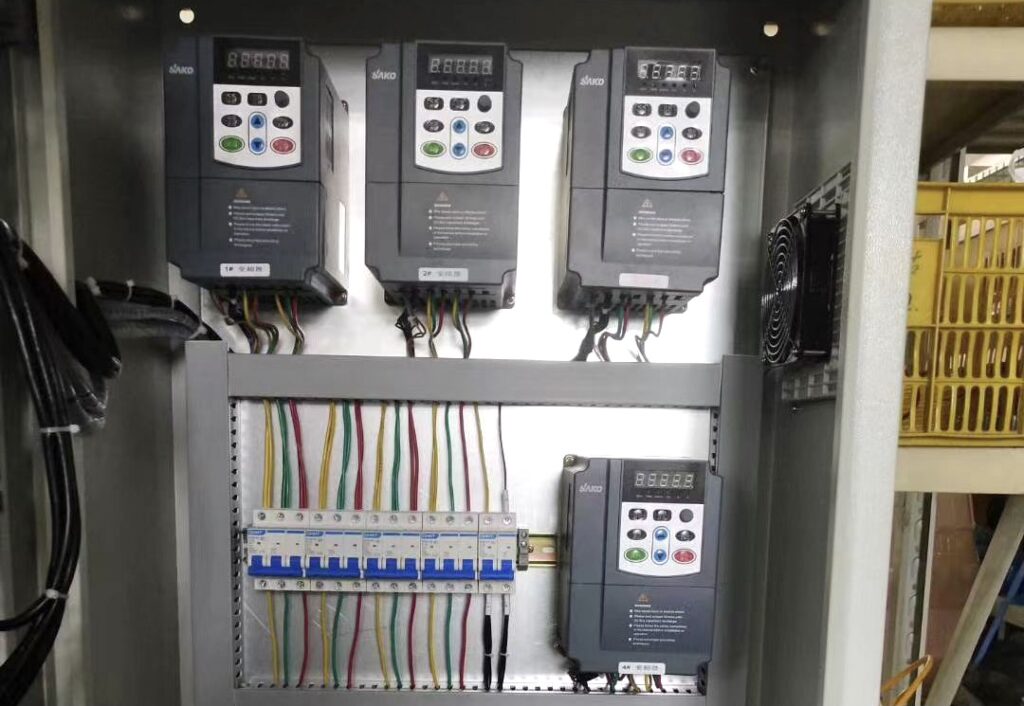
Why Are VFDs Essential in Motor Start-ups?
Traditional motor starters, like the Direct-On-Line (DOL) starters, initiate motor operation with a sudden jolt of dc voltage. This instantaneous application of voltage to the motor can cause stress to the equipment.
Here are the differences between DOL starters and VFD starters.
DOL (Direct-On-Line) Motor Start
Impact on the Grid: DOL starting introduces a sudden inrush of current to the motor. This can cause voltage dips in the electrical supply network, affecting other connected devices and potentially leading to temporary brownouts.
Impact on the Motor: The instant application of full voltage to the motor can cause mechanical and electrical stress. Over time, repeated DOL starts can lead to premature wear and potential damage to the motor windings.
Impact on the Shaft String: A sudden start can produce high torque that can stress the shaft. This can result in misalignment, increased vibration, and even potential mechanical damage to the connected machinery or equipment.
VFD (Variable Frequency Drive) Motor Start
Smooth Starting, resp. Ramping up the Motor Speed with VFD: VFDs control the frequency and voltage supplied to the motor, allowing for a gradual increase in speed. This eliminates the sudden inrush of current, ensuring a soft start that reduces mechanical and electrical stress on the motor.
VFD Decouples the Motor from the Grid: By using a VFD, the motor's operation is isolated from direct grid disturbances. This means fluctuations or abnormalities in the grid voltage won't directly impact the motor, ensuring more stable and reliable motor operation.
Input Power Factor is Independent of Motor Power Factor: One of the advantages of a VFD is that it can maintain a high input power factor, regardless of the motor load. This is achieved by drawing current in a sinusoidal manner. This property aids in reducing reactive power in the system, ensuring more efficient power utilization and less strain on the electrical network.
VFDs gradually ramp up the motor speed, preventing the mechanical stress associated with abrupt starts. Moreover, by optimizing the current drawn during start-up, we can significantly reduce the risk of inrush currents. Why does this matter? Well, inrush currents can often exceed the motor's rated current by six to eight times, potentially causing damage.
Why Are Smooth Start-ups So Important?
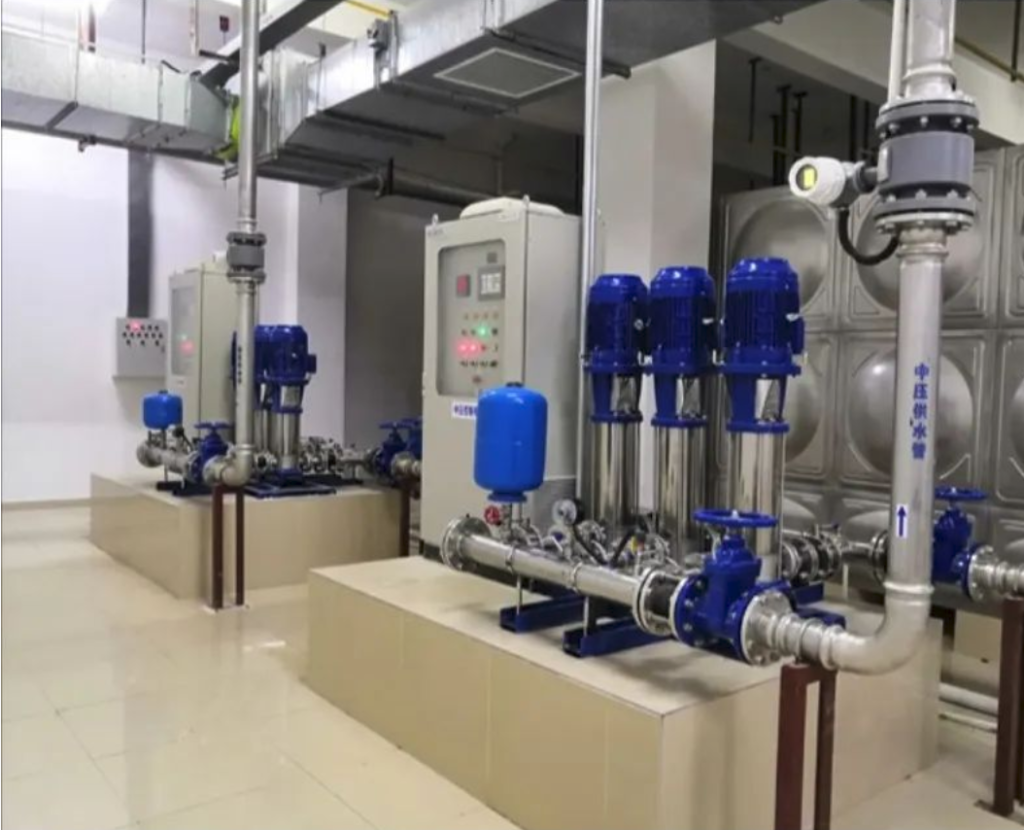
Think of motor start-up as awakening a sleeping giant. If you startle it, there's a greater chance it might act erratically or get damaged. The same principle applies to motors. Abrupt start-ups can lead to wear and tear, reducing the longevity of ac motors and the equipment.
Additionally, soft starts via VFDs eliminate the risk of water hammer in pump applications. This phenomenon occurs when fluid in motion is forced to stop or change direction suddenly, causing a surge of pressure in the pipeline. Over time, this can lead to damage or even failure of the pipeline.
What is the starting current of a VFD motor?
When using a VFD, the starting current for electric motor is roughly 1.5 times the full-load current of the motor, a value that's four times lower than with cross-line starting. Although the VFD method grants enhanced control and flexibility when starting the motor, it's more expensive.
Does VFD reduce starting current?
Yes, a VFD reduces the starting current of a motor by gradually ramping up the voltage and frequency, allowing for a smoother and less stressful start-up compared to direct starting methods.
Does a VFD replace a motor starter?
Yes, a VFD can replace a motor starter in many applications.
While a motor starter is primarily used to turn a motor on or off and provide overload protection, a VFD not only starts and stops the motor but also controls its speed and torque by varying the motor's input frequency and voltage. When a VFD is used, there's often no need for a separate motor starter, as the VFD provides both ac motor with starting and protective functions. However, in some installations, a basic motor starter or contactor might still be used in conjunction with a VFD for isolation or other specific reasons.
Are There Energy Savings with VFDs?
Absolutely! At SAKO, our VFD department has consistently witnessed the energy-saving prowess of these devices. By allowing motors to run only at the needed speed, VFDs can save up to 50% in energy costs compared to other start-up methods.
Consider this: a pump or fan running at half speed consumes only one-eighth of the energy compared to one running at full speed. It’s all thanks to the cube law of centrifugal loads. So, not only do VFDs help in reducing mechanical stress, but they also pave the way for considerable further energy consumption reduction.
Are There Any Additional Advantages?
Certainly! VFDs are versatile. Beyond soft start-ups and energy savings, they offer precise speed and torque control. This level of control is especially crucial in processes where the product quality might get affected by variations in motor speed or torque.
Additionally, VFDs can also reverse the motor direction without the need for additional switches. The benefits are manifold: from increased process efficiency to improved product quality. Plus, their digital interfaces allow easy integration with modern control systems, offering enhanced monitoring and control capabilities.
So, Should Every Motor Use a VFD?
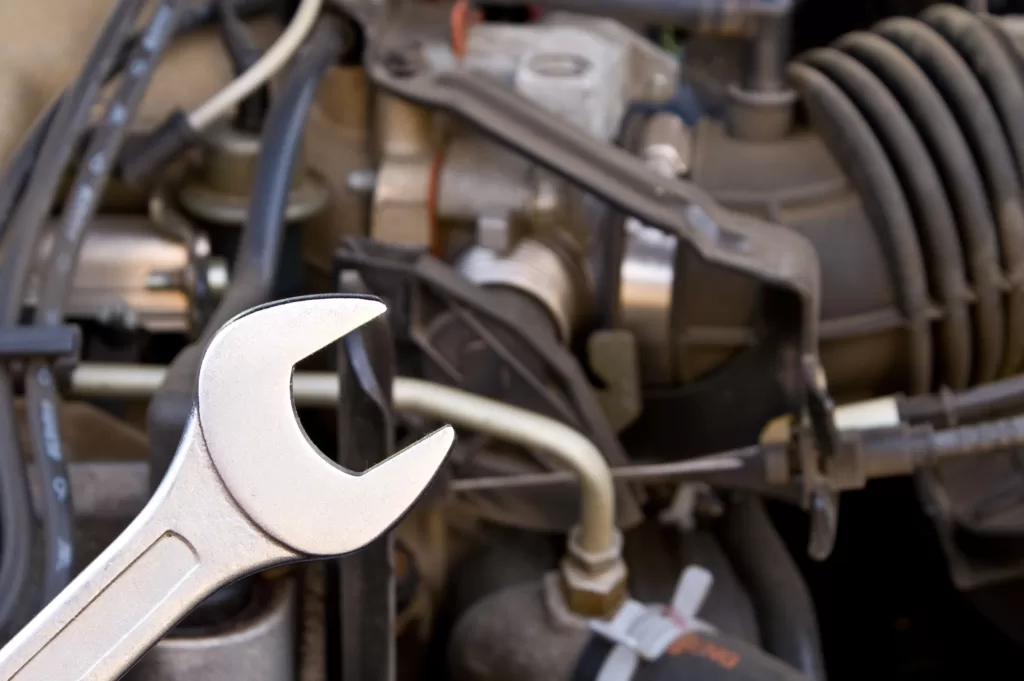
While VFDs offer numerous benefits, they might not be suitable for every application. Motors that run continuously at full speed or those that don't need speed control might not benefit as much from VFDs.
However, in applications where speed control, energy efficiency, savings, and equipment longevity are paramount, VFDs are the undisputed champions.
Conclusion
VFDs have revolutionized motor start-ups, offering benefits that span from smooth operations to energy savings. As the General Manager of foreign trade at SAKO’s VFD department, I've witnessed their transformative impact firsthand. While they may not be the answer for every application, their advantages in the right settings are undeniable.