Speaking from personal experience, I often encounter clients who are curious about how VFDs (Variable Frequency Drives) function within a pumping system. This curiosity is typically driven by a need to enhance efficiency and control in various applications. I must confess, understanding the way VFDs operate can open doors to exceptional flexibility and savings. Allow me to walk you through this fascinating technology that we, at SAKO, specialize in, and explore how it can redefine the way you operate your pumps.
VFDs are essentially controllers that drive electric motors by varying the frequency and voltage supplied to the motor. By modulating the speed of the electric motor itself, VFDs enable pumps to run only at the speeds required, thereby conserving energy and providing more precise control over the process.
Intrigued? Allow me to dive into the nitty-gritty and answer some of the most common questions we get about this groundbreaking technology.
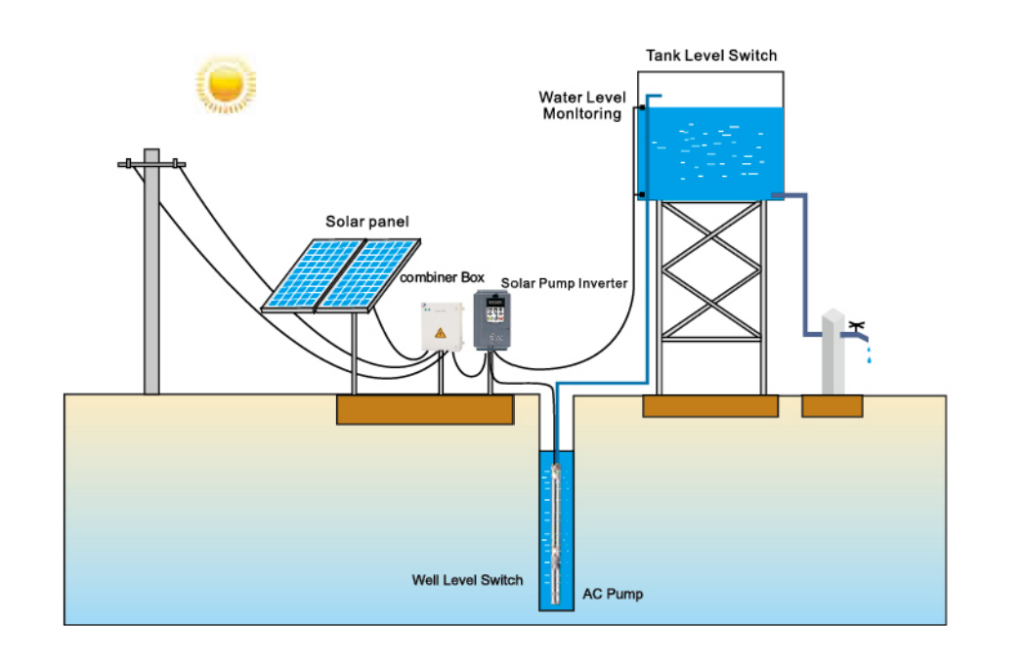
How Exactly Does a VFD Function in a Pumping System?
A VFD’s role in a pump is multi-faceted. Firstly, it controls the frequency of the electrical power supplied to the pump motor. By doing so, it regulates the motor’s speed and ensures that the pump operates only at necessary speeds.
Boldly put, the energy savings this provides is considerable. A VFD-controlled pump can reduce energy output power consumption by up to 30%. This can translate into substantial cost savings for businesses.
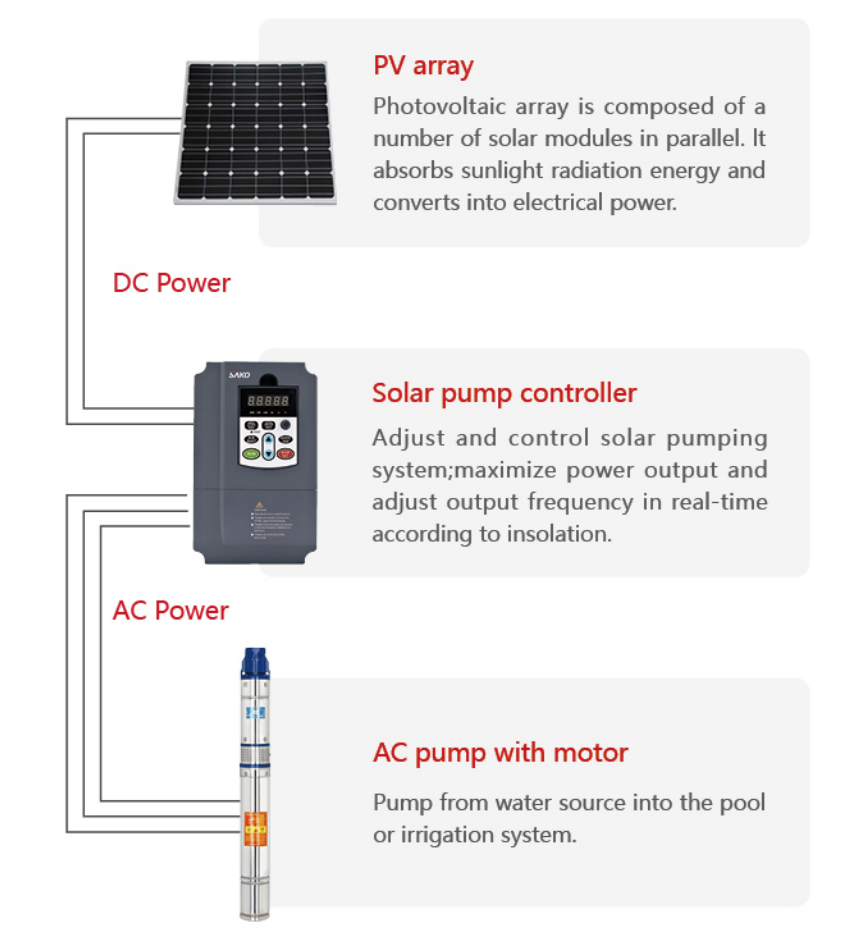
What Are the Benefits of Using VFDs in Pumps?
Utilizing Variable Frequency Drives (VFDs) in pumps has revolutionized the way industries manage flow control and energy consumption. The integration of VFDs with pumps offers a plethora of benefits that cater to the demands of modern industrial applications. Here’s a detailed breakdown of these advantages:
1. Energy Efficiency
One of the most compelling benefits of using VFDs in pumps is the significant reduction in energy consumption. By precisely controlling the speed and flow rate of the pump, VFDs optimize the pump curve energy usage, leading to a potential reduction of up to 30% in energy costs, according to a study.
2. Improved Process Control
VFDs enable accurate control of parameters like flow rate and pressure, allowing for a more stable and reliable process. This adaptability ensures that the pump operates at optimal power and efficiency, catering to the exact needs of the application.
3. Extended Equipment Life
By soft-starting the motors, VFDs reduce the stress on the mechanical components of the motor speed the pump. This not only enhances the lifespan of the equipment but also minimizes maintenance requirements, saving both time and money.
4. Reduction in Water Hammer
The controlled acceleration and deceleration of the pump provided by VFDs help to minimize the phenomenon known as water hammer. This leads to increased system reliability and reduces the risk of damage to pipes, valves and other equipment.
5. Flexible Operation
VFDs provide flexibility in operations by allowing adjustments to flow rates and pressures according to the demand. This adaptability is particularly beneficial in applications where variable speed and varying conditions are common, enabling a more responsive and efficient system.
6. Cost Savings
Beyond energy efficiency, pump VFDs contribute to overall cost savings. The reduction in maintenance, extended equipment life, and potential for incentives from energy-saving programs further bolster the financial benefits of using VFDs in pumps.
7. Environmental Benefits
The energy savings associated ac power used with VFDs translate into a reduced carbon footprint, making it an environmentally friendly choice. By optimizing energy consumption, industries can contribute to sustainability goals and adhere to environmental regulations.
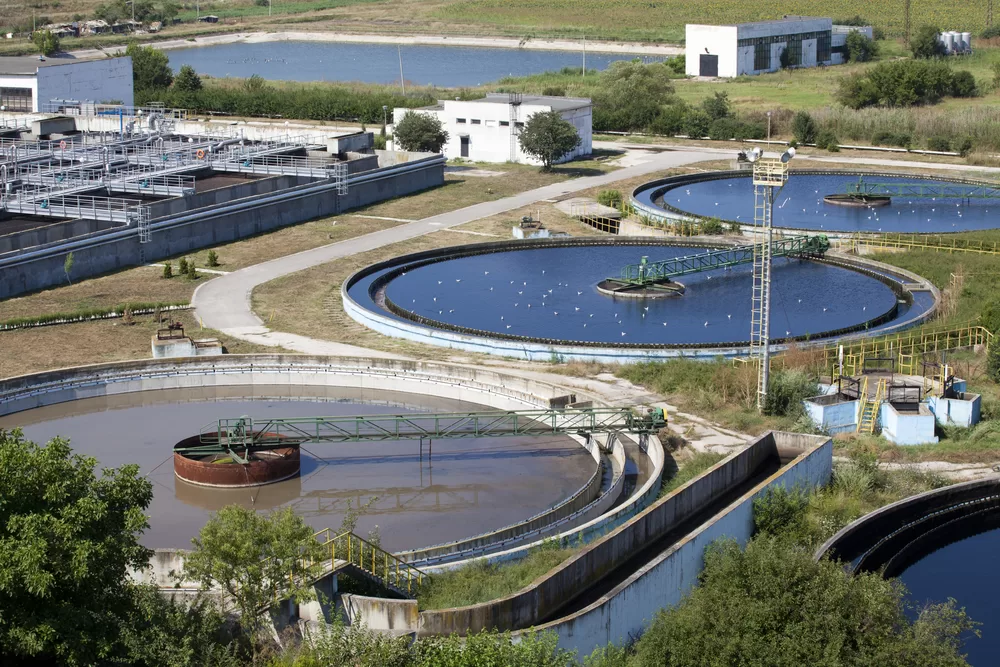
Applications of Variable Frequency Drives (VFDs) in Various Pump Systems
Here’s an overview of the types of pumps where VFDs might be used:
- Centrifugal Pumps: These are commonly found in water supply applications, HVAC systems, and industrial process systems. By using a VFD, the flow rate can be adjusted to meet the specific demand.
- Submersible Pumps: Often used in wastewater management, irrigation, or mining applications, VFDs in submersible pumps can help control the flow and pressure.
- Positive Displacement Pumps: These include types such as gear, lobe, and screw pumps, and are used in applications where a constant flow rate is needed regardless of the pressure. VFDs can provide better control and efficiency.
- Turbine Pumps: Used in deeper wells and higher pressure applications, VFDs can help control the speed and flow of these pumps, improving efficiency and performance.
- Diaphragm Pumps: These are often used in chemical applications. Using VFDs can provide better control over the flow and prevent over-pressurization, which can be critical in handling hazardous materials.
- Booster Pumps: In water distribution systems, VFDs can be used in booster pumps to ensure constant water pressure regardless of the varying demand.
- Slurry Pumps: Used in mining, wastewater, and other industrial applications to handle abrasive materials, VFDs can control the flow and reduce wear on the pump components.
- Swimming Pool Pumps: Even in more domestic settings like swimming pools, VFDs can provide energy savings by allowing the pump to run at reduced speeds when the demand is lower.
- Fire Pumps: While not as common, some fire protection systems might use VFDs to control the water pressure and flow in response to varying fire protection needs.
- Hydraulic Pumps: In applications requiring precise control over fluid flow and pressure, such as manufacturing or hydraulic machinery, VFDs can improve responsiveness and accuracy.
In conclusion, VFDs can be used in a wide range of pumps across various industries, including water and wastewater treatment, industrial processes, mining, agriculture, and more.

How to Choose the Right VFD for Your Pump?
Choosing the correct Variable Frequency Drive (VFD) for your pump system is a vital decision that can significantly affect the efficiency and reliability of your pump operation throughout. Here’s a comprehensive guide to help you select the perfect VFD for your pump:
1. Understand the Pump Requirements
First and foremost, understand the specific needs of the pump system. Is the application demanding constant or variable torque? What’s the required flow rate and pressure? These considerations lay the foundation for selecting the right VFD.
2. Evaluate the Motor Compatibility
It’s crucial to assess whether the VFD is compatible with the motor type used in your system. Check the motor specifications such as horsepower, voltage, phase, and speed to ensure that the VFD can properly take input power and control it.
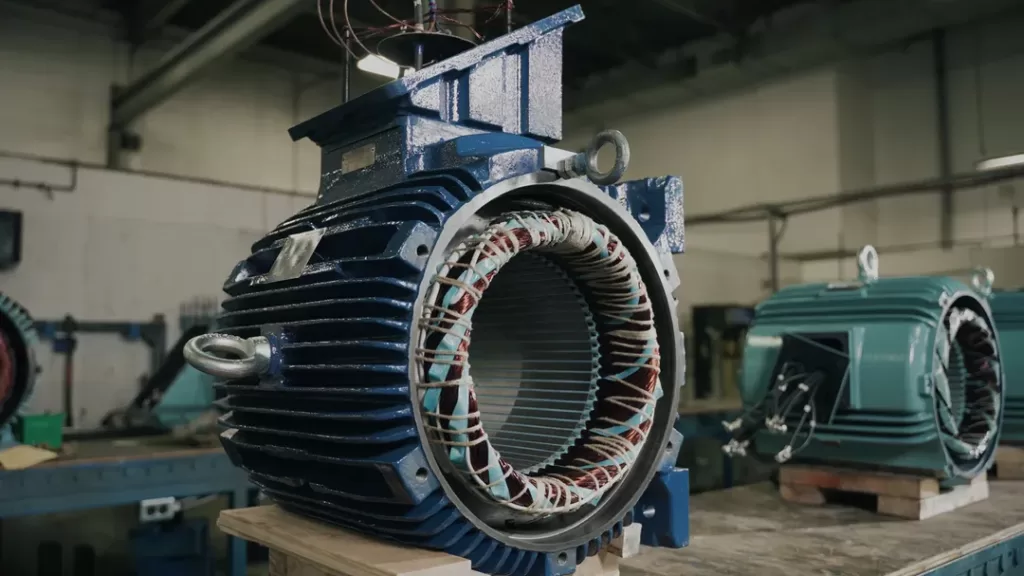
3. Consider the Operating Environment
The environment in which the VFD will operate can affect its performance. Factors like temperature, humidity, and dust must be considered. Select a VFD with the appropriate enclosure and cooling method to withstand environmental conditions.
4. Assess Control Features and Communication Needs
Different VFDs offer varying levels of control features and communication options. Consider what kind of control system demand is needed for your pump system, such as remote monitoring or integration with other devices. Check for compatibility with communication protocols if network integration is required.
5. Calculate the Total Cost of Ownership
Beyond the initial purchase price, evaluate the total cost of ownership. This includes installation costs, energy savings, maintenance requirements, and potential rebates or incentives available in your region.
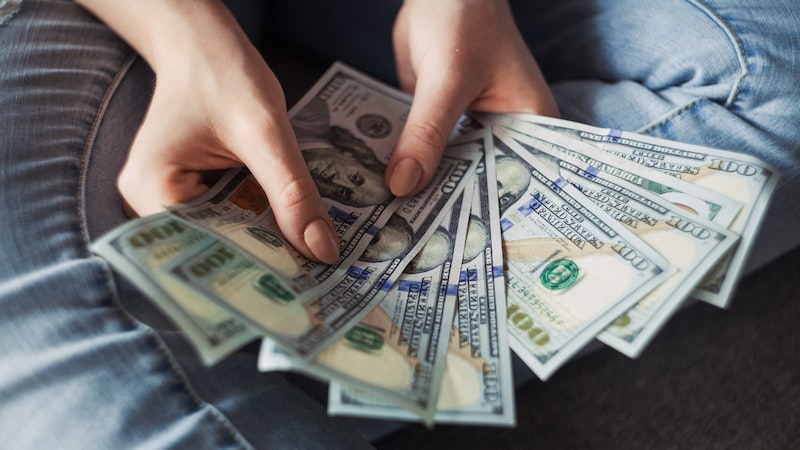
6. Consult with a Professional
When in doubt, consult with a professional or a reputable supplier like us at SAKO. Our extensive experience in providing tailored VFD solutions can guide you to the perfect match for your system, ensuring optimal performance and efficiency.
Conclusion
The integration of VFDs with pumps offers a comprehensive set of benefits that align with the contemporary industrial landscape. From energy efficiency and process control to cost savings and environmental stewardship, the use of VFDs in pumps is a transformative solution that continues to shape the way industries operate.
As the General Manager of Foreign Trade at SAKO’s VFD department, I’ve witnessed the profound impact that VFDs have had on pump operations across various sectors. Feel free to reach out to our team at SAKO for more insights or personalized solutions tailored to your needs.