In the field of industrial automation, inverters are essential devices that allow precise motor speed control to meet various production process requirements. Among the diverse range of inverters, two commonly mentioned types are heavy-duty inverters and vector inverters. But are they the same? Let’s dive deeper into the differences between these two types of inverters.
1. Definition and Principles
Heavy-Duty Inverters
As the name suggests, heavy-duty inverters are designed specifically for high-power applications. They are mainly used in industries that require large motors to run under full load or even overload conditions for extended periods. Common industries include mining, metallurgy, cement, and paper manufacturing.
Heavy-duty inverters typically use more robust power modules and cooling systems to ensure reliable performance even during prolonged high-load operation. These inverters are optimized with algorithms that provide superior overload protection while maintaining system stability.
Vector Inverters
Vector inverters, on the other hand, are based on vector control technology. This advanced motor control method decouples the motor’s magnetic field from its torque, allowing for precise control over both the motor’s speed and torque.
Vector inverters can break down the motor’s stator current into magnetizing and torque components, enabling control over both independently. This results in greater torque at low speeds, improved dynamic performance, and higher speed control accuracy, making them ideal for industries such as CNC machinery, elevators, and textile machines.
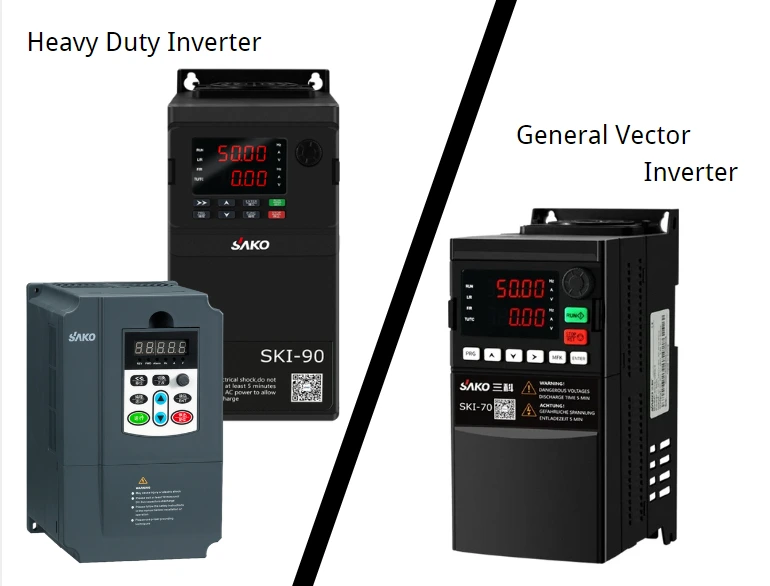
2. Performance Characteristics
Heavy-Duty Inverters
- Strong Overload Capability: These inverters can handle sustained motor overload, often rated for 150% or more, which is a key distinction from standard inverters.
- High Reliability: Designed for harsh industrial environments, heavy-duty inverters use high-quality components and have robust protection mechanisms to ensure stable operation.
- Adaptability to Tough Conditions: They perform well under extreme conditions, such as high temperatures, humidity, and dust, making them suitable for industries like mining and manufacturing.
Vector Inverters
- High-Precision Speed Control: Vector inverters offer wide speed ranges and exceptional control accuracy, often with ratios as high as 1:1000, maintaining precise performance throughout the range.
- Excellent Dynamic Performance: They respond quickly to changes in acceleration, deceleration, and load, ensuring smooth motor operation and increasing production efficiency.
- High Torque at Low Speeds: Even at low speeds, vector inverters provide high torque, making them ideal for heavy-load startups in devices such as cranes and hoists.
3. Application Scenarios
Heavy-Duty Inverters
These inverters are mainly used in industries where motors require high power and operate under tough conditions, such as:
- Mining: Equipment like crushers, conveyors, and hoists need high-power motors that frequently run under full load in dusty, humid conditions.
- Metallurgy: Steel rolling mills and electric furnaces have high load requirements and demand exceptional overload capacity.
- Cement: Cement mills and fans operate for long hours under heavy loads, and heavy-duty inverters meet these demands.
Vector Inverters
Vector inverters are best suited for applications that demand precise speed and dynamic performance, such as:
- CNC Machinery: These inverters provide accurate control of motor speed and position, ensuring high machining precision and surface quality.
- Elevators: Elevators require smooth starts, accelerations, and stops. Vector inverters ensure precise motor control for a comfortable and safe ride while improving energy efficiency.
- Textile Machines: Textile production demands high precision and fast dynamic response to ensure product quality, both of which are met by vector inverters.
4. Relationship and Differences Between the Two
Relationship
Heavy-duty and vector inverters are not entirely separate concepts; there is some overlap. Some vector inverters have strong overload capabilities and can be used in heavy-duty applications. Similarly, some heavy-duty inverters may incorporate vector control technology to enhance performance.
Differences
- Design Focus: Heavy-duty inverters prioritize overload capability and reliability to ensure stable long-term operation in demanding environments. Vector inverters focus on speed control accuracy and dynamic performance.
- Control Algorithms: Vector inverters are built around vector control technology for decoupling the motor’s magnetic field and torque. Heavy-duty inverters, however, are more focused on overload protection and stability.
- Application Fields: Heavy-duty inverters are primarily used in heavy industries such as mining and metallurgy. Vector inverters are used in precision applications like CNC machines, elevators, and textile equipment.
Conclusion
In conclusion, heavy-duty inverters and vector inverters are distinct in their design, principles, performance, and applications. When choosing an inverter, it’s important to consider the specific requirements of your equipment and production environment. For high-load, harsh environments that demand strong overload capabilities, heavy-duty inverters are the ideal choice. On the other hand, if your application requires high precision in speed control, dynamic performance, and low-speed torque, vector inverters will better suit your needs. In some cases, a combination of both technologies may be necessary for more complex industrial automation needs. Understanding the differences between these inverters will help you make informed decisions for optimizing your industrial processes.