When diving into the world of water pumps and variable frequency drives, I often find myself bombarded with questions about the intricacies of these systems. I’ve been fortunate to spearhead the foreign trade efforts for the VFD department at SAKO, which has given me unique insights into this topic. One question that I hear time and again is: “How many kilowatts at minimum does a water pump need to have to require the installation of a frequency converter?”
For most applications, a water pump doesn’t inherently “need” a VFD based on kilowatts alone. Rather, the decision hinges more on operational requirements, energy-saving objectives, and the desire to control and modulate flow rates. However, for industrial applications, pumps with capacities starting from 3kW and above often benefit the most from a VFD.
Why? Well, let’s dive deeper to unwrap this puzzle and make sense of when and why to integrate VFDs into your pumping systems.
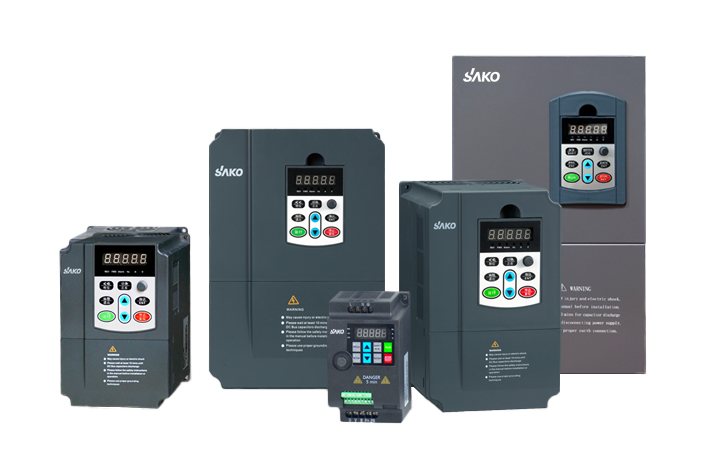
why do pumps with capacities starting from 3kW and above often benefit the most from a VFD? To understand this, we need to delve into the advantages of VFDs and their applicability to larger pumps.
Energy Savings:
VFDs regulate the motor’s speed and power usage. Pumps with higher capacities, such as those over 3kW, often have higher operating costs due to their energy consumption. By using a VFD, the pump only consumes the energy it requires, based on demand, which can lead to significant energy savings.
For smaller pumps, while there are still energy savings, the absolute monetary savings might be less compelling due to the lower power consumption to start with.
System Protection & Longevity:
Higher capacity pumps can experience damaging issues like water hammer or mechanical stress during start-up and shut-down processes. VFDs allow for a soft start and gradual stop, reducing the mechanical stress on the system and extending the pump’s lifespan.
In smaller systems, these stresses might be less pronounced, making the VFD’s impact on longevity less critical.
Improved Process Control:
In industrial or commercial settings where larger pumps are common, precise flow control is often crucial. VFDs provide this by continuously adjusting the pump speed to maintain the desired flow or pressure.
In smaller domestic systems, this level of precision might be overkill or not as noticeable to end-users.
Reduction of Peak Demand Charges:
In many industrial and commercial settings, users are billed based on their peak energy demand. Starting a large pump can cause a significant spike in energy usage. VFDs, with their soft-start capability, can mitigate these peaks, leading to cost savings on energy bills.
This is less of a concern for smaller pumps, which don’t create the same demand spikes.
Flexibility:
In variable applications where the demand can change, such as in processing plants, VFDs offer the flexibility to adjust operations without needing to stop and start the pump manually or change pulleys.
Smaller pumps are often in more consistent demand situations, making this flexibility less of a selling point.
Maintenance Costs:
Larger pumps, given their size and the strain of moving large volumes of liquid, can incur significant wear and tear, especially if they’re continually started and stopped. VFDs can reduce these wear-and-tear cycles, leading to longer intervals between maintenance and reduced costs.
Smaller pumps inherently have less wear and tear due to their lower capacities.
In summary, while smaller pumps can still benefit from VFDs in certain situations, the combination of energy savings, extended equipment lifespan, improved process control, reduced peak demand charges, flexibility, and decreased maintenance costs make VFDs especially advantageous for pumps with capacities starting from 3kW and above.
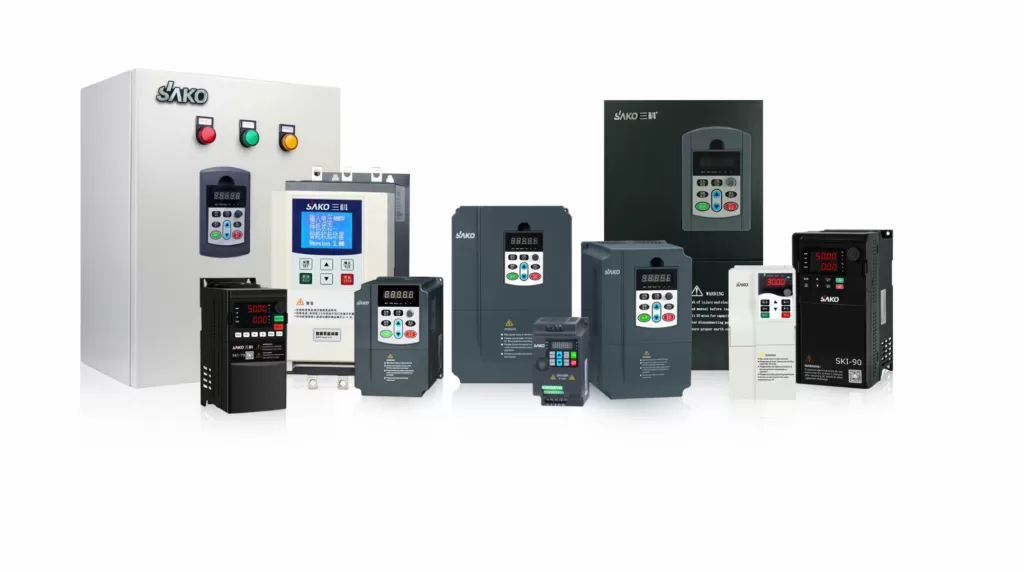
How to Size a VFD for a Pump: A Comprehensive Guide
When it comes to optimizing pump efficiency and energy savings, the integration of a variable frequency drive (VFD) is paramount. However, choosing the right VFD for pump operation involves many factors. This guide will help navigate the complexities of VFD sizing for pumps.
Understanding the Pump and Motor Relationship
The pump motor is the heart of any pump model. Pump manufacturers design pumps to work at their best efficiency point, but pump operating conditions vary. Often, pump motors aren’t operated at their rated speed, resulting in potential energy savings being left on the table. Recognizing the relationship between pump performance, pump head, flow rate, and the speed of the pump is essential.
Centrifugal vs. Positive Displacement Pumps:
Centrifugal pumps and positive displacement pumps operate differently. While a centrifugal pump’s efficiency relates closely to its flow rate, positive displacement pumps maintain efficiency regardless of flow. It’s crucial to recognize which type you’re working with.
Key Factors in VFD Sizing
1. Motor Specifications:
Dive into the pump motor’s specifications. Motor manufacturers provide crucial details like power, rated speed, and minimum speed. Keep an eye out for the motor’s efficiency point, as operating pumps beyond this can lead to increased energy cost.
2. Minimum and Maximum Speeds:
Never run pump motors below their specified minimum speeds. Low speeds can lead to increased temperature rise in motor windings, and for centrifugal pumps, low flow can lead to pump damage. Conversely, never exceed the maximum speed set by pump manufacturers; this ensures motor efficiency and extends pump life.
3. Operating Point:
Your pump curve and system curve should intersect at the operating point. This point is the duty point, where the pump’s rotational speed meets the system’s flow demands. If the pump operating point doesn’t align with the best efficiency point, VFDs can help adjust the pump’s speed motors to save energy.
4. Energy Savings Potential:
Variable speed operation, facilitated by VFD systems, allows pumps to operate closer to their best efficiency point. The affinity laws provide a mathematical relationship between speed, power, and flow, highlighting potential energy savings when operating at reduced speed.
5. Understand Static and Dynamic Head:
Pump head consists of static head and dynamic head. While static head remains constant, dynamic head varies with flow rates. A proper VFD operation ensures pumps can adjust to changes in dynamic head, ensuring pump efficiency.
Other Considerations
1. Torque Requirements:
Centrifugal pumps require variable torque drives. In contrast, positive displacement pumps often need constant torque drives or constant torque VFDs. Understanding the pump’s torque needs is vital for selecting the correct VFD system.
2. Communication and Integration:
Modern VFD systems often come with digital output capabilities, enabling integration into broader system controls.
3. Environmental Factors:
Consider temperature rise, potential pump damage at low flow conditions, and isolated bearings which might be sensitive to certain VFD operations.
4. Harmonics:
VFD operation can introduce electrical noise or harmonics. Some motor windings, especially in submersible pumps, can be sensitive to this. VFD manufacturers often provide solutions like filters or isolated bearings to mitigate these issues.
Final Thoughts
Sizing a VFD for a pump is a holistic process. Many factors, from the pump curve to motor efficiency, play a role. While the pump manufacturer provides a performance curve, the particular system in place introduces system losses that can impact the pump running conditions. Consulting with us SAKO,the VFD manufacturers is recommended to ensure the best VFD selection for energy-saving benefits. Remember, a well-sized VFD system can result in energy savings, improved pump efficiency, and prolonged pump life.
If you find the selection of a variable frequency drive challenging, please feel free to consult with us.